機械部品の熱処理・表面処理基礎講座
本講座(全8章50講座)では、機械部品に用いられている金属材料(主に鉄鋼材料)の種類と、それらに適用されている熱処理(焼なまし、焼入れなど)および表面処理(浸炭・窒化処理、めっき、PVD・CVDなど)について、概略と特徴を紹介します。
7-9 溶射の種類と適用
溶射とは、燃焼炎または電気エネルギーを用いて溶射材料を加熱し、溶融またはそれに近い状態にした粒子を物体表面に吹き付けて皮膜を形成させる表面処理法です。溶射材料には金属、セラミック、サーメット、プラスチックなど広範囲のものが適用できます。
溶射作業では、図1に示すように、溶射材料は燃焼炎や電気的放電によって急速に加熱されて溶融または半溶融状態の粒子になり、この粒子は圧縮空気などによって加速されて処理物表面に叩きつけられて付着し、処理物によって冷却されます。この現象が繰り返されて溶射材料が堆積し、所定の皮膜が形成されます。
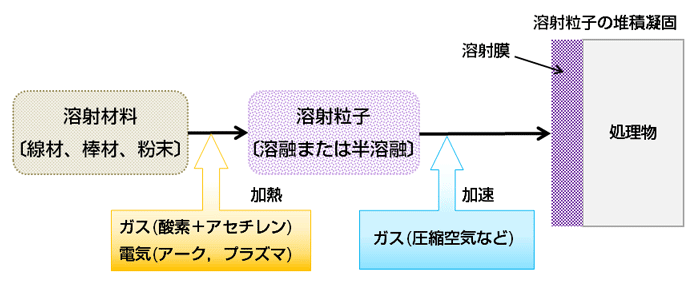
図1 溶射膜形成の模式図
一例として、図2にガスフレーム溶射によって生成した鉄系皮膜の表面形態と断面組織を示します。表面形態は、溶融した溶射粒子が勢いよく叩きつけられて周辺に広がった様相を呈しています。また、断面組織からは、溶融した金属粒子が潰れて扁平状になって堆積している様相が見られます。この断面組織から、溶射膜は溶融した粒子が潰れて扁平状になったもの、溶融しないで球状のままの粒子、各粒子表面付近の酸化物(灰色部)および多数の空孔(黒色部)から構成されていることが分かります。
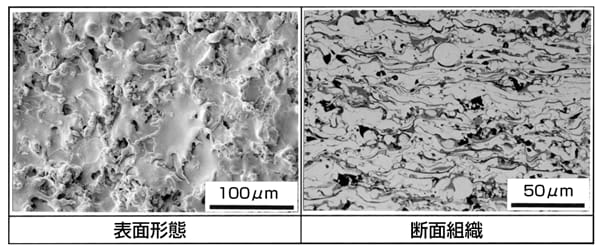
図2 ガスフレーム溶射によって生成した鉄(Fe)系皮膜の表面形態および断面組織
溶射法は図3に示すように、熱源の種類によってガス式と電気式に大別されます。これらはさらに加熱形態によって細分化されており、用いられる溶射材料の種類や形態、処理物の種類や形態によって使い分けられています。
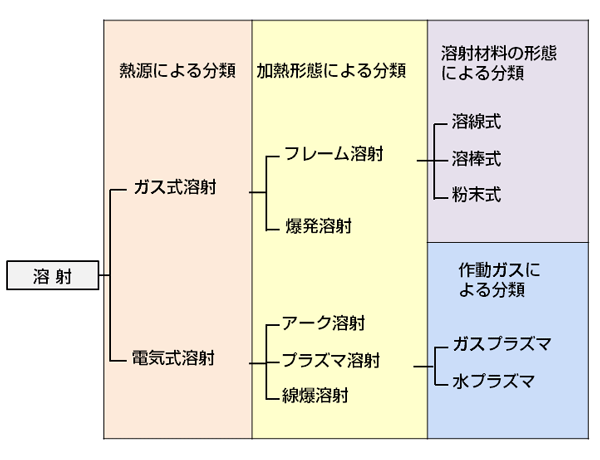
図3 溶射の分類
ガス式溶射には、フレーム溶射と爆発溶射があります。フレーム溶射は、燃料ガス(通常はアセチレンと酸素の混合ガス)による燃焼炎を熱源とするものです。溶射法の中でも適用できる溶射材料の形態および種類が多岐にわたっており、形態では線、棒および粉末が、種類では金属、セラミック、樹脂など広範囲の溶射に用いられています。爆発溶射は、燃料ガス(アセチレン+酸素)の爆発燃焼によって溶射材料を溶融加速して皮膜を形成させるもので、密着性の優れた緻密な皮膜が得られます。
電気式溶射にはアーク溶射、プラズマ溶射および線爆溶射があります。アーク溶射は、溶射材料である2本の金属線の先端でアークを発生させて溶融し、溶融した粒子を圧縮空気で基材に吹き付けて皮膜を形成させるものです。プラズマ溶射は、溶射材料を高温プラズマジェットによって溶融・加速して基材に皮膜を形成させるものです。プラズマの温度は10000℃以上にも達しますから、セラミックや高融点金属材料の溶射によく用いられています。線爆溶射は、金属線に瞬時に高電圧を印可して溶融爆発させ、高速で溶融金属を飛散させるもので、パイプなどへの内面コーティングに適しています。
溶射には金属系溶射、セラミック溶射、サーメット溶射、プラスチック溶射など多種多様のものがあり、JISでも表1に示すように種々の溶射について規定しています。最初に工業的規模で利用された溶射は亜鉛溶射であり、その目的は鉄鋼材料に対する防錆防食です。その後、アルミニウムやそれらの合金溶射が行われるようになり、大気環境で使用される建造物や各種タンク類を中心に利用例が増加しています。
表1 JISによる溶射の種類
種類 | 適用溶射法 | JIS番号 | |
---|---|---|---|
亜鉛,アルミニウム及びそれらの合金溶射 | Zn,Al,AlMg,ZnAlなど | 溶線式フレーム溶射 アーク溶射 |
JIS H 8300 |
肉盛溶射 | ステンレス鋼(CrNi,CrNiMo),低炭素鋼(Mn,MnSi),高炭素鋼(MnSi,MnCrTi),低合金鋼(MnCrTi),ニッケルクロム鉄合金(NiCrFe)など | 溶線式フレーム溶射 | JIS H 8302 |
粉末式フレーム溶射 | |||
アーク溶射 | |||
自溶合金溶射 | NiBSi,NiCuBSi,NiCrBSi,CoCrNiMoBSi,CoCrNiWBSi,NiCrCuMoWBSiなど | 粉末式フレーム溶射 | JIS H 8303 |
プラズマ溶射 | |||
セラミック溶射 | アルミナ(Al2O3),酸化チタン(TiO2),酸化クロム(Cr2O3),酸化ジルコニウム(ZrO2)、酸化アルミニウム・酸化クロム(Al2O3,)など | プラズマ溶射 | JIS H 8304 |
粉末式フレーム溶射 | |||
溶棒式フレーム溶射, | |||
サーメット溶射 | 炭化タングステン・コバルト溶射(WC/Co),炭化タングステン・ニッケル溶射(WC/Ni)など | プラズマ溶射 | JIS H 8306 |
粉末式フレーム溶射 |
肉盛溶射は、主に機械部品に対して耐摩耗性、耐食性、耐熱性などの付与を目的として行われています。溶射材料としては、炭素鋼、低合金鋼、ステンレス鋼などがあり、それらは使用目的や溶射適用材に応じて細分化されています。
金属系溶射の一つである自溶合金溶射は耐食性、耐熱性、耐摩耗性を付与する目的で行われています。この溶射の特徴は溶射後に再加熱して溶融する(フュージング)ことであり、この溶融処理によって熱拡散による基材との密着性が向上し、空孔をほとんど無くすことができます。溶射材料としては、ニッケル(Ni)基及びコバルト(Co)基の金属系のもの、それらの合金に硬質の炭化タングステン(WC)を配合したものなどが適用されています。
セラミック溶射は耐摩耗性、耐薬品性、耐熱・断熱性などを付与することを目的として行われています。溶射用セラミックの種類は酸化アルミニウム、酸化チタン、酸化クロム、酸化ジルコニウムなどで、これらが単独または混合されて用いられています。
『機械部品の熱処理・表面処理基礎講座』の目次
第1章 機械部品に用いられる材料
-
1-1機械材料の種類と分類機械を構成している材料は、総称して機械材料と呼ばれています。機械材料は図1のように、金属材料、非金属材料および複合材料に分類できます。
-
1-2鉄鋼材料の種類と分類鉄鋼材料は、合金元素の添加や熱処理によって物理的性質や機械的性質を容易にコントロールすることができます。
-
1-3鉄鋼とは鉄鋼材料の主成分は鉄(Fe)であり、そのほかに必ず含まれる元素があります。
-
1-4純鉄の結晶構造金属は、原子が規則正しく配列した結晶であり、その配列の仕方によって種々の結晶構造が存在します。
-
1-5鉄鋼の温度と金属組織の関係(鉄―炭素系平衡状態図)鋼の基本は鉄(Fe)と炭素(C)との合金であり、含有する炭素量によって各温度における金属組織は異なります。
-
1-6鉄鋼の冷却速度と特性の関係(連続冷却変態)前回解説した鉄―炭素系の平衡状態図は、鉄鋼材料を扱う者にとっては重要ですが、熱処理作業においては連続冷却変態曲線のほうがもっと重要です。
-
1-7鉄鋼の等温保持による特性の変化(等温変態)前回は、オーステナイト領域から連続冷却したときの変態について説明し、熱処理との関係を示しました。
第2章 鉄鋼製品に実施されている熱処理の種類とその役割
-
2-1熱処理の種類と分類熱処理とは、適当な温度に加熱して冷却する操作のことを言い、鉄鋼材料はこの操作によって所定の機械的性質や耐摩耗性が付加され、個々の持っている特性が引き出されます。
-
2-2完全焼なましと焼ならしの役割完全焼なましは、機械構造用炭素鋼および機械構造用合金鋼にはよく適用される処理で、主な役割は組織の調整と軟化です。
-
2-3球状化焼なましの役割球状化焼なましは、炭素工具鋼(SK)、合金工具鋼(SKS)および軸受鋼(SUJ)には必須の熱処理です。
-
2-4応力除去焼なましの役割低温焼なましは、溶接、鋳造、冷間加工などによって生じた残留応力を除去し、軟化や焼入変形の軽減を目的として行われるもので、加熱温度はA1変態点以下です。
-
2-5焼入れと焼戻しの役割焼入れの目的は二つあり、機械構造用鋼と工具鋼とでは異なります。機械構造用鋼に対する目的は、高い強度を付与することであり、焼入れ後に施す焼戻しとの組み合わせによって、要求される機械的性質を得るための前処理として位置づけられています。
-
2-6等温熱処理の種類と役割等温変態曲線を利用した熱処理は等温熱処理とよばれ、同等の金属組織が得られる通常の熱処理よりも、短時間処理が可能なこと、熱処理にともなう変形が少ないこと、機械的性質の優れたものが得られることなど、多くの利点がある熱処理法です。
第3章 機械構造用鋼の焼入れ・焼戻し
-
3-1機械構造用鋼の種類と分類機械部品に多用されている機械構造用鋼は、機械構造用炭素鋼、機械構造用合金鋼、焼入性を保証した構造用鋼がJISに規定されています。
-
3-2熱処理条件と金属組織機械構造用鋼の持っている最高の特性を発揮させるためには、理想的には焼入れによって完全なマルテンサイト組織にすることです。
-
3-3熱処理条件と硬さの関係硬さは機械的性質を決める基本ですから、熱処理を依頼する際には、硬さ指定するのが普通です。しかも、その硬さは焼入れと焼戻しとの組み合わせで決まりますから、それらの条件設定は非常に重要です。
-
3-4熱処理条件と機械的性質の関係機械構造用鋼にて作製した機械部品に要求される特性は、引張強さやせん断強さと同時に衝撃に強いことです。これらの特性は、材質によっても異なりますが、一般には焼入れ焼戻しによって調整されています。
-
3-5硬さと機械的性質の関係前項までに記述したように、機械構造用鋼の硬さや機械的性質は焼戻温度に依存していることが明らかです。
-
3-6焼入性と合金元素の関係焼入後の硬さの値は表面からの測定値で表しますが、鋼種によっては内部硬さが全く異なることも多々あります。
-
3-7質量効果と合金元素の関係前回紹介した焼入性とは、鋼材そのものの特性ですから、JISによって試験片の寸法・形状、焼入加熱温度が規定されていますし、焼入冷却は試験片の一端からの噴射冷却で、そのときの冷却速度は無限大が前提になっています。
第4章 ステンレス鋼とその熱処理
-
4-1ステンレス鋼の種類と用途ステンレス鋼はCrを11%以上含有した鋼で、金属組織の違いによって、オーステナイト系、オーステナイト・フェライト系(二相系)、フェライト系、マルテンサイト系および析出硬化系に分類されています。
-
4-2オーステナイト系ステンレス鋼の熱処理オーステナイト系ステンレス鋼は、焼入れによって硬くして、引張強さを高めることはできません。
-
4-3マルテンサイト系ステンレス鋼の熱処理マルテンサイト系ステンレス鋼は、図1に示すように焼入れによってマルテンサイト組織が得られ、低温焼戻しによって優れた耐摩耗性とじん性が付与されますから、耐食性も重視した機械構造用部品、医科用機械部品、刃物および金型などに多用されています
-
4-4析出硬化系ステンレス鋼の熱処理析出硬化系ステンレス鋼は、SUS630とSUS631の2種類がJISで規定されています。表1に示すように、両鋼種とも固溶化熱処理後(熱処理記号:S)に析出硬化熱処理を行い、所定の強度を付与して使用されます。
第5章 非鉄金属材料とその熱処理
-
5-1アルミニウム合金とその熱処理アルミニウムおよびアルミニウム合金には、展伸材と鋳物材があります。展伸材とは、圧延加工した板や条、展伸加工した棒や線のことをいいます。
-
5-2銅合金とその熱処理銅は有色金属で色合いが美しく、切削加工や塑性加工が容易で、しかも鋳造性も良好なため、鉄よりも遥かに古くから使用されています。
-
5-3チタン合金の熱処理チタンは、密度が鉄の約1/4ですから軽量金属材料として分類されており、しかも比強度が高く、耐食性も優れています。
第6章 機械部品に対する表面処理の役割
-
6-1清浄と表面処理表面処理を適用する場合、汚れが付着したままでは、密着不良になるだけでなく、正常な処理層が得られないなどの不具合を生じてしまいます。
-
6-2防錆・防食と表面処理腐食には、乾式による腐食(乾食)と湿式による腐食(湿食)とがあり、機械部品においてとくに問題になるのは後者です。
-
6-3着色と表面処理着色は、表面処理の種類によっては代表的な利用目的であり、図1に示すように、着色法には塗装、印刷およびPVDなど物理的方法、薬品による表面反応や加熱による酸化を利用する化学的方法、電気めっきや陽極酸化など電気化学的方法があります。
-
6-4摩擦摩耗特性と表面処理機械部品において、使用中に相手との摩擦をともなう箇所では、必ず摩耗が発生しますから、耐摩耗性を付与するために種々の表面硬化処理が利用されています。
-
6-5耐疲労性と表面処理疲労(疲れ)とは、物体が繰返し応力を受けた際に、その応力が物体の持つ引張強さよりも小さい応力であっても、徐々にき裂が発生・進展していくことで、最終的には破壊してしまいます。
第7章 機械部品を対象とした主な表面処理
-
7-1表面処理の種類と分類表面処理とは、製品や部品の表面を何らかの方法で処理加工することで、表1のように分類することができます。
-
7-2表面焼入れの種類と適用表面焼入れとは、鋼の変態点以上(オーステナイト領域)まで急速に加熱し、内部温度が上昇する前に急速に冷却して表面だけ硬化させるものです。
-
7-3浸炭/浸炭窒化処理の種類と適用浸炭とは、炭素含有量の少ない鋼を浸炭剤中でオーステナイト領域の高温(900℃位)に加熱し、表面から炭素(C)を拡散浸透させることです。
-
7-4窒化/軟窒化処理の種類と適用窒化処理は、表1に示すように、工業的にはガス窒化から始まり、塩浴を用いる方法やプラズマを用いる方法など多くの方法が開発され、広範囲の分野で採用されています。
-
7-5金属元素の拡散浸透処理の種類と適用金属元素の拡散浸透処理は、主に鋼を対象として耐食性や耐熱性の付加を目的として利用されています。
-
7-6電気めっきの原理と適用電気めっきとは、めっきしたい金属イオンを含む水溶液中で、めっき処理品を陰極(-極)、めっきしたい金属を陽極(+極)として電解するものです。
-
7-7無電解めっきの原理と適用無電解めっきは、電気を使わないで化学反応によって皮膜を析出させますから、化学めっきともよばれています。
-
7-8溶融めっきの原理と適用溶融めっきとは、溶融金属中に処理物を浸漬して表面に溶融金属の皮膜を形成させるものです。
-
7-9溶射の種類と適用溶射とは、燃焼炎または電気エネルギーを用いて溶射材料を加熱し、溶融またはそれに近い状態にした粒子を物体表面に吹き付けて皮膜を形成させる表面処理法です。
第8章 機械部品の損傷と調査法
-
8-1機械部品の破損の種類金属製品の損傷には、物理的因子によるものと化学的因子によるものがあります。
-
8-2機械部品の破壊に及ぼす因子金属製品の破壊に及ぼす因子としては、図1に示すように、金属製品自身の問題と使い方の問題があります。
-
8-3機械部品の熱処理欠陥熱処理欠陥には多くの種類がありますが、初期損傷として発覚することが多いので、その大部分は使用する前に露見します。
-
8-4破損品の原因調査手順破損とは物理的因子によって生じる損傷で、その現象には破壊、変形および摩耗があります。
-
8-5マクロ観察による破壊形態の確認破壊原因を特定するためには、破面を観察することは当然ですが、いきなり走査型電子顕微鏡(SEM)によってミクロ観察するのではなく、はじめにマクロ観察によって破面の状況を十分に把握しなければなりません。
-
8-6ミクロ破面の観察による破壊形態の確認破面のミクロ観察は通常走査型電子顕微鏡によって行われています。破壊には結晶粒界に沿って亀裂が進行する粒界破壊と結晶粒内を進行する粒内破壊があります。
-
8-7機械部品の破損事例(脆性破壊)脆性破壊を生じる要因としては、硬質部品におけるエッジ箇所の存在、材料不良や熱処理不良、めっき時の水素の侵入、残留応力など種々のものがあげられます。
-
8-8機械部品の破損事例(疲労破壊)疲労破壊とは、繰返し負荷される荷重によって破壊するもので、とくに機械部品には最も多く発生するものです。
-
8-9機械部品の破損事例(めっき品のトラブル)機械部品は主に耐食性を付加するために、亜鉛(Zn)めっきをはじめ種々のめっきの適用事例が多いのですが、同時にめっき品に発生する不具合も多々あります。