塗料・塗装の何でも質問講座
4-16 VOC削減型塗料-粉体とはどんな塗料なのか
1.粉体塗料の事始め
粉体塗装の事始めは鉄鋼をイオン化傾向の大きい亜鉛で被覆する金属溶射である。 溶射とは金属を(例えば、亜鉛を加熱して)溶かしながら圧縮空気と混合させて加熱粒子として、鉄鋼にくっつけるエアスプレー法である。 噴霧された金属粒子は目標以外の箇所にも付着するから、仕上がり外観が悪くなる。仕上がり性を良くするのであれば、溶かした亜鉛(液体)を浴に入れて鉄鋼を浸せきさせる方が良い。後者の方法を溶融亜鉛メッキ法と呼ぶが、金属を粒子として付着させる方法ではないから、粉体塗装の事始めにならない。 金属溶射の次に出て来た方法はポリエチレン(PE)粉体を亜鉛と同様にして、圧縮空気に乗せて加熱溶融させ、金属に吹き付ける方法である。大沼氏4)によると、これが1948年に行われたので、図4-34に示すように、日本における粉体塗装の事始はPE粉体と言われている。 初期の粉体塗装はフレームスプレー法4)と呼ばれ、ポリマーの溶融流動状態は十分ではないから、後加熱が必要であった。
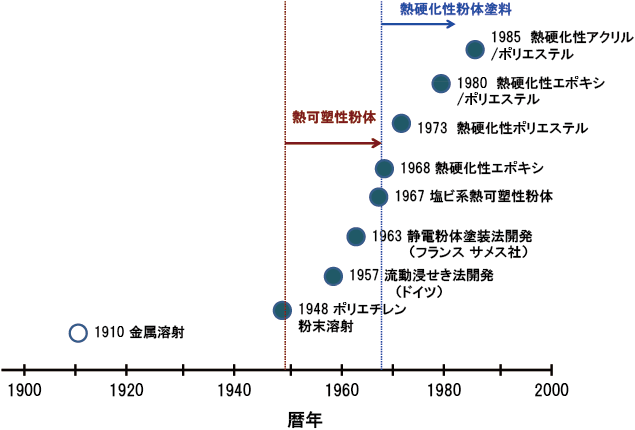
1957年にはドイツで、図4-35に示す流動浸せき法が開発された。 ポリマー粒子槽に0.1MPa程度の圧縮空気を流し、ポリマー粒子を流動状態にしておき、この中に加熱した被塗物の金属を入れ、ポリマー粒子を溶融させる。 さらに、今日の塗装スタイルであるコロナ帯電式静電粉体塗装法は1962年にフランスのサメス社で開発された。 日本における粉体塗料の流れは図4-34に示すように、熱可塑性(チョコタイプ)樹脂から出発し、1970年頃から熱硬化性(クッキータイプ)樹脂粉体が開発され、1980年には、粉体の代表選手であるエポキシ/ポリエステル系ハイブリッド粉体塗料が上市された。 2019年度に年間生産量は4万tに達したが、塗料全体での構成比は3%に達していない。 本来ならばもっと伸びても良いのに、なぜ、伸び悩んでいるのかについても考えたい。
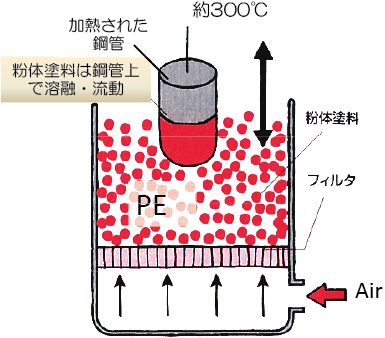
2.粉体塗料が一般塗料と異なる点とは
2.1 原料はすべて粉体(固体)である
原料として、図4-36(a)に示すように、一般に液体成分を使用しない。 固体成分の樹脂を溶融させて練り合わせる。 混練とも呼ぶように、単純に混合するだけになる。 しかも、熱硬化性樹脂を使用するから硬化剤も固体であり、溶融して混練される。 最近、使用量が多いウレタン硬化ポリエステル粉体塗料には-NCOをブロックした硬化剤が使用されている。 ブロック剤の解離温度は170℃であるから、焼付温度を180℃以上にせざるを得ない。 塗料化するときには主剤の樹脂が溶融しなければならず、混練時の温度を100℃程度にしている。
次に、図4-36(b)に示す製造工程を説明する。 まず、初めに温度をかけないで原料をかき混ぜる予備混合を行い、樹脂を溶融させるエクストルーダーに入れる。 樹脂が溶融すると、各原料が混練されて、流動物になる。これを煎餅のように引き延ばし、冷却して粉砕し、ペレットにする。 さらに、ペレットを粉砕し、平均粒径40μm程度の粉体を調製し、篩(ふるい)通しを行って、粉体塗料になる。
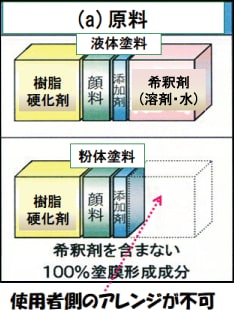
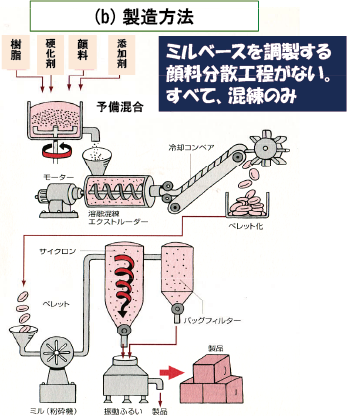
2.2 粉体塗料の混合で調色ができない
調色は混練時に複数顔料の配合(重量分率)で可能だが、エクストルーダーの仕様により、小ロットや特注色の対応は難しい。 液体塗料であれば、調色用原色ベースがあるから小ロットでも、広範囲な特注色でも対応できるが、粉体塗料では単色である赤、白の粉体塗料同士を混合しても、ピンクにはならない。このように粉体塗料の混合で、調色ができず、需要が伸びない一因でもある。
2.3 顔料分散工程が無いため、顔料充てん濃度が低くなる
調色は溶融混練時であれば可能であり、粉体塗料の適合する被塗物はガスボンベやガードレールのような大きなロットで、微妙な色違いを問題にしない物がよい。 一方、液体塗料では分散工程で、顔料濃度の高いミルベースを調製し、顔料濃度を低めた調色ベースを作る。 これらは図4-37に示すように顔料が良好に分散されており、含量の異なる調色ベースとも良く混ざり合い、ほぼ均一な色味になる。 顔料を扱う色材分野では顔料分散は大切な工程である。
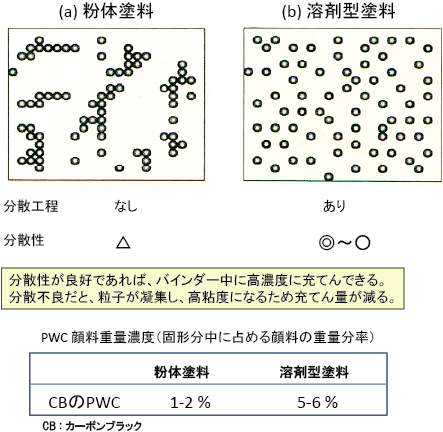
2.4 粉体にとってのシンナー作用は空気が行う
塗料にとって貯蔵安定性は大切な特性である。 静電塗装時に粉体塗料の付着性(帯電性)が悪くなり、粒子の流動性の低下により異物が発生する時がある。 このような時には、粉体塗料に強制的に空気を流し、篩(ふるい)通しを行うと良い。 以前の良好な状態に復帰できることがある。 僅かな粒子の凝集で帯電特性や流動性が劣化しやすい。 この時の粉体に対する空気の作用は、溶剤型塗料におけるシンナーの作用と同等である。 なお、篩(ふるい)通しを行う際に、粉体塗料にアルミナやシリカの微粒子を添加すると良い。 1μm程度の添加微粒子が40μm程度の粉体粒子表面に吸着し、+イオンになる。この作用で静電塗装時に-イオンの空気の吸着量が増え、帯電性能が向上すると考えられる。 この効果は、高湿度下で粉体粒子の帯電性能が低下した時に顕著に現れるらしい。
2.5 架橋前の樹脂のTgは高い方が良い
保管中に砂糖や塩が固まるように、粉同士が凝集して固化する現象をブロッキングと呼ぶ。 夏場に保管中の温度が40℃以上になったら起きやすい。 できるだけ30℃以下で保管することが大切である。2.4で述べた現象はブロッキングの初期と考えて良い。
塗料物性から考えた耐ブロッキング性の対策として、架橋前の樹脂のTg を60℃程度にすることが有効である。 保管中に粒子同士の接触で、粒子の軟化を防ぐことができるからである。 架橋前の樹脂のTg を上昇させるためには、エポキシ樹脂やフェノール樹脂のように環構造を多く含有する樹脂を選択すると良い。 しかし、架橋後には硬くて脆い塗膜になる心配がある。 この対策として、図4-38に示すジャングルジムの目の粗さを粗くして、たわみ性を持たせることにする。
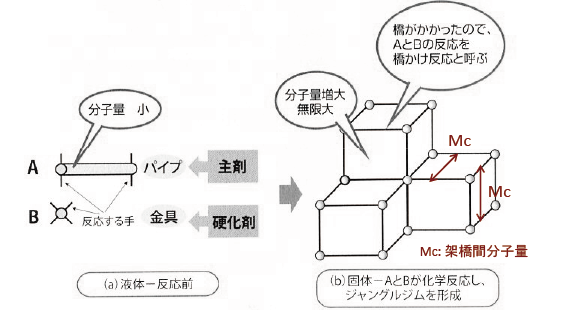
2.6 1回塗り仕上げが可能である
塗装は基本的に図4-39に示すように、下塗り、中塗り、上塗りで仕上げられる。 塗装効果は各層の機能が総合されて発現する。 新車塗装では約100μmの膜厚に塗装効果が集約されているから、この塗装系に粉体を登場させようとすると相当高いハードルが課せられる。
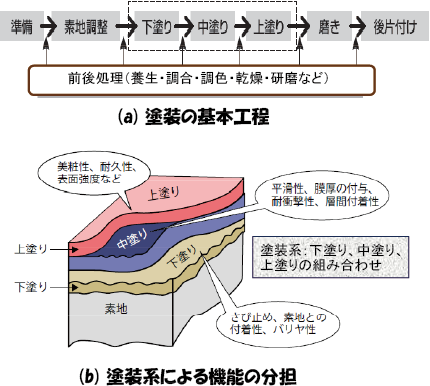
表4-9に示すエアコン室外機ボックスの塗装仕様を見ると、採用塗料の種類で塗装工程が変わる。 粉体塗料では1回塗り仕上げが可能である。 1回塗りで40~50μmの膜厚を塗り、溶融過程でエポキシ樹脂が被塗物界面に移行する粉体塗料もある。 このように粉体塗料は1回塗りで塗装効果を発現することを得意にしている。 さらに、粉体塗料はVOCをゼロと見なせること、危険物ではないこと、静電粉体塗装機を使用すれば技能要素が要らないことなど、メリットは多いが、需要増に結びつかない。 前述した粉体塗料の調色の他に、もっと、核心に迫る欠点がある。
表4-9 塗装系と塗装仕様2)
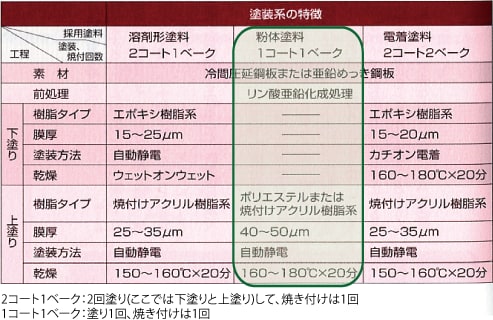
粉体塗料は平均粒径40μm程度の粒子であり、被塗物に付着した帯電粒子は溶融過程でレベリングしても、液体塗料の様に均一で平滑な塗り肌にはなりにくい。 この事がネックになり、新車の塗装ラインにおいては、粉体塗料が上塗りクリヤに採用されていない。 また、粉体塗料の1回塗りは得意であるが、塗装系の一部を分担するのは難しい。 塗装ブースも別になり効率的ではない。 水性塗料では塗装後にFlash offが必要であるが、粉体塗料ではFlash offなしで、塗装後に焼付けできることなど、液体塗料と粉体塗料の差異が歴然としてくる。 著者は粉体塗料の需要を伸ばすためには、次の考えが必要だと考える。
我々は粉体を全く新しい環境対応型塗料であると認識し、専用の塗装ラインを構築する考えで臨む必要がある。 このような取組をせずに塗料の1種として使用しようとしても上手く行かない。 一方で、現有設備を活用できるならば、水性で良いという考えが浸透しているから、粉体塗料の需要が伸びないのも事実である。 実用面から見た環境対応型塗料の比較を表4-10に示す。 この比較表からも判るように、粉体塗料は従来の塗装法では手に負えないし、既存の設備を使えないことも理解できる。
表4-10 実用面から見た環境対応型塗料の比較
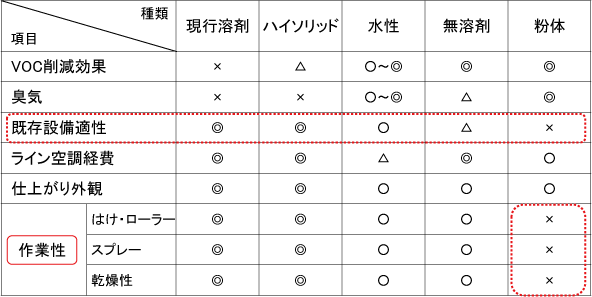
〔引用・参考文献〕*4章通し番号
1)大藪泰:表面技術, Vol.70, No.5, p.236-241 (2019)
2)職業能力開発総合大学校編:“塗料”, 雇用問題研究会, p.15, 18, 126 (2007)
3)工藤雄一郎・四柳嘉章: 植生史研究 第23巻 第2号 p.55-58 (2015)
4)大沼清利:“技術の系統化調査報告”, 国立科学博物館, Vol.15, March (2010)
5)前川浩二:“第52回塗料入門講座”講演テキスト, (社)色材協会 関東支部 (2011)
6)フリー百科事典『ウィキペディア(Wikipedia)』, 玉虫厨子
7)http://msatoh.sakura.ne.jp/08053site.htm
茶の湯の森 (nakada-net.jp)で検索してください。
8)https://boku-undo.co.jp/story/st2.html
9)エチルアルコールと水の密度をそれぞれ0.79、1.0g/cm3、酒のアルコール濃度を16wt%として、酒の密度を計算した。
10)https://4travel.jp/travelogue/10116454
11)日本塗料工業会データを一部参照
12)坪田実、高橋保、長沼桂、上原孝夫:塗装工学, Vol.36, No.6, 213-222 (2001)
13)中道敏彦、坪田実:“トコトンやさしい塗料の本”, 日刊工業新聞社, p.39,55,91,155 (2008)
14)坪田実:塗装技術、理工出版社、2011年4月号、p128-134 (2011)
15)アネスト岩田株式会社80年史 (2005)
16)坪田実:“工業塗装入門”, p.27, 日刊工業新聞社(2019)
17)R.H.Kienle, C.S.Ferguson:Ind.Eng.Chem., 21,349 (1929)
18)坪田実:色材, 91, No.8, p.282 (2018)
19)坪田実:学位論文“塗膜物性に及ぼす顔料効果の研究”, 東京大学, p.202 (1985)
20)坪田実:“図解入門塗料と塗装の基本と実際”, 秀和システム, p.57,75 (2016)
21)武井昇:“旭サナックテクニカルレビュー2014”, p.2 (2014)
22)日本塗料工業会ホームページ:http://www.toryo.or.jp/jp/info/index.html
23)大澤悟:建材試験センター 建材試験情報 5月号(2014)
24)シーエムシー出版編集部:“塗料開発の新展開”, シーエムシー(2022)
『塗料・塗装の何でも質問講座』の目次
第1章 塗料・塗膜の白化現象
-
1-1白く見えるとはどんなこと塗装面に現れる白化には水分が関与して、発生することが多々あります。
-
1-2散乱強度と隠ぺい力前回の図1-4は白黒がはっきりした良い結果でした。ポリマーと屈折率の差が小さいCaCO3粒子を分散させた塗膜は粒子/ポリマー界面で可視光線の多くは
-
1-3隠ぺい力に関する話題実際の塗装作業においては、図1-10(b)に示すように、下地が透けるため何回も上塗りをしたことがあります。
-
1-4塗装時に白化する現象とその解析 (1) 結露の発生高温多湿な梅雨時にスプレー塗装をすると、かすみがかかったように白くぼけてつやが無くなることがあります。
-
1-5塗装時に白化する現象とその解析 (2) 結露の防止結露とは空気中から水分が抽出される現象だと理解しました。
-
1-6水性塗料の白化現象とその対策木工用の水性ボンドは身の回りの接着剤としてよく使用されています。
-
1-7木工塗装テーブル面の白いシミ(1)前回までは塗装時や塗装過程での白化現象を取り上げましたが、今回と次回は我が家で起きた木工テーブル面の白化現象を取り上げます。
-
1-8白いシミの原因とは白化機構を示した前回の図1-30に妥当性があるかどうかを見極めたいと思います。
-
1-9白いシミの再現と解析実験前回示した図1-35の結果についてコメントすると次のようになります。
-
1-10白いシミの対策法質問(30)前回のQ&Aを読んでいると、白化の原因は塗膜中へ侵入した水がZn粒子/バインダー界面へ偏析することであり、白化にはガラス転移温度Tgの影響が大きく、
第2章 塗料と塗装のことはじめ
-
2-1塗料の必要条件と分類法第1章では塗料・塗装分野で見られる白化という欠陥現象を取り上げ、原因と対策を話してきたのに、第2章で何故「ことはじめ」になるのですか。
-
2-2塗料(液体)から、塗膜(固体)への変化前回から持ち越した (1)塗料の形態による分類、(4)塗膜なってからの分類法について解説してください。
-
2-3自動車補修塗装に必要な材料と器工具について(1)質問(10) 本章に対する著者の考え方については、既報2.1に示す答え(1)で示されていますが、いきなり自動車補修塗装とは、入門者にとって何だか難しい応用問題を与えられたようです。
-
2-4自動車補修塗装に必要な材料と器工具について(2)質問(20) フェンダー部打痕部の板金修正が終わったら、次はどうするのですか。答え(20) 打痕部面積の5倍程度大きく塗膜をはがし、鋼板素地を露出させます。
-
2-5自動車補修塗装工程について(1)今回も自補修塗装を取り上げます。板金修正で凹んだ箇所を引張り出し(既報図2-20)、塗膜をはく離した鋼板露出面(既報図2-22)からスタートします。
-
2-6自動車補修塗装工程について(2)前回は、ポリパテ付け作業で終了しています。図2-11に示すStep3とは、パテ付け面の研磨までを指します。パテ付け、研磨作業までが元の板金面に復活させる成形作業になります。
-
2-7自動車補修塗装工程について(3)前回は、Step4(図2-11参照)のプラサフ塗装とその研磨について解説しました。その中で、ブツ除去時やパテ研磨時にできる小穴を見逃さないためのガイドコートの使い方を説明しました。
-
2-8自動車補修塗装工程について(4)前回は、上塗りのブロック塗りとスポット塗りについて説明しました。ほとんどの場合、上塗りにはクリヤが塗装されます。
-
2-9スプレーガン-名手への道(1) ガンの基礎知識車の補修塗装ではスプレーガンの技能が大切だと言うことを理解できたと思います。
-
2-10スプレーガン-名手への道(2) ガンを使いこなすStep既報2.5~2.7に示した車の補修塗装で、プラサフ塗装を始め、ボカシ塗り技法を含めたスプレーガンによる塗装技術を紹介しましたが、実際にどのようにやれば良いのか分からなかったと思います。
第3章 いろいろな塗り方
-
3-1塗装方法を知ろう建築現場における塗装作業に注目すると、図3-1に示すように外壁を仕上げるのに、窓枠の養生をしている人、ローラ塗りをしている人、吹付け作業をしている人など様々です。
-
3-2液膜転写法塗装方法を大別すると、図3-4に示すように、塗料を直接、被塗物に移行する直接法と、微粒子の霧にして移行する噴霧法になります。
-
3-3直接法 はけ塗り前報の図3-4に示したように、塗装方法は直接法と噴霧法に大別されます。高速塗装に適する方式は、直接法の液膜転写法です。今回、紹介する方法は直接法で工具を介して塗る刷毛塗りとローラー塗りを取り上げます。
-
3-4直接法 はけ塗り刷毛の代表例を図3-13に示します。5)塗料の種類、塗り面積等に応じて適切なはけを選びます。一般に合成樹脂調合ペイントのように粘度の高い塗料では硬い毛(黒い馬毛)のずんどう刷毛を、ウレタンワニスやラッカーのように粘度の低い塗料では、やわらかい毛(白い羊毛)のすじかい刷毛を用います。
-
3-5直接法 ローラー塗りローラー塗りは刷毛塗りと工具が違うだけで、塗り方の基本は刷毛塗りと同じです。仕上がり面の平滑性は、はけ塗りに劣りますが、住宅の壁などの広い面積を塗るのに適しており、作業スピードは刷毛塗りに比べて3倍程度大きいようです。
-
3-6直接法 浸せき塗り、しごき塗り浸せき塗りは、次に示す2方式に大別されます。1つ目は、塗料槽に被塗物をどっぷり浸け、引き上げて乾燥させるDipping方式(浸せき塗り、ジャブ漬け塗りなど)です。2つ目は、被塗物に塗料を押し込むしごき塗りです。
-
3-7電着法 電着塗装の原理電気化学をベースとする塗装法が電着塗装です。水の電気分解を理解すれば、電着塗装の原理がわかります。
-
3-8電着法 前処理工程-化成被膜自動車に代表される工業塗装では、電着塗装を行う前に、前処理として、洗浄・脱脂・化成皮膜処理が行われます。
-
3-9電着法 電着塗装工程電着塗装装置の構成は一般的に次のようになります。
-
3-10噴霧法 静電気と静電塗装スプレーガンによる微粒化の原理とガンの使い方に付いては、第2章 2.9と2.10スプレーガン名手への道で解説しました。本節では、噴霧塗装に静電気を利用すると、塗着効率が2倍以上も増大すると言う話を紹介します。
-
3-11噴霧法 静電スプレーと塗料の電気抵抗値前回、静電スプレーは雷と同じ原理を利用していることを説明しましたが、液体塗料の電気抵抗値が静電スプレー作業において、どのような影響を及ぼすかについては言及しませんでした。
-
3-12噴霧法 粉体塗料の塗り方塗料メーカーは粉体塗料を平均粒径30-40μmに調製して、供給しています。液体塗料をこの程度の噴霧粒子にするためには空気霧化だけでは不十分で、遠心力で液体分子を引きちぎったりしなければなりません。
-
3-13噴霧法 粉体塗料の塗り方(つづき)今回は電界内を大量に移動しているフリーイオンの挙動に焦点を当て、塗装作業との関連について説明した後、コロナ放電式以外の塗り方について説明します。
第4章 塗料のルーツと変遷
-
4-1はじめに執筆中の「塗料・塗装の何でも質問講座」はこの第4章から後半戦に入ります。本講座の終了時点で、読者の皆さんにはペンキのことをよく知ってもらい、風呂場や床などの住環境を塗り替えたり、自分で作った工作物を塗って仕上げるまでになってもらえたら嬉しいなと思います。足場が必要な高所はプロのペンキ屋に任せればよいのです。
-
4-2塗料のルーツについてルーツ探しは誰もが興味を持っていますが、塗料・塗装のルーツとはと聞かれると、現代人は“塗料って何だ”と言って、あまり興味を示してくれないでしょう。一方、旧石器時代の方々に身振り手振りで塗料とは液状のもので、指や手にとって、彼方此方に塗るものだと伝えると、ものすごく理解が速いと思います。
-
4-3紀元後~飛鳥・奈良時代大沼清利氏は塗料の変遷をバインダー(被膜になる成分で、ビヒクルソリッド)に着目して克明にまとめ、国立科学博物館発行の「技術の系統化調査報告 第15集(2010)」に、“塗料技術発展の系統化調査”として報告しています。
-
4-4平安時代(日本最古の黒エナメル)図4-3に示す塗料の歴史の中に、平安時代に武器である楯(たて)と戟(げき)に塗る黒色エナメルの配合表が見つかりました。図4-6に示します。4)日本最古の塗料のレシピと言われています。奈良時代に作られた墨と同様に掃墨と膠が使用されています。
-
4-5鎌倉~戦国・南蛮貿易~江戸時代さて、今回も表4-2の続きになりますが、戦国時代から江戸時代における塗料の変遷を追って行きます。戦国時代には出土品や文化財がほとんどなく、歴史的事実だけから塗料・塗装の変遷を探ることになります。仏教伝来後、漆は仏像や寺院建築に使用され発展して行くと同時に、戦国大名の武具にも塗られていたようです。庶民の生活レベルでは、ニカワ(膠)、柿渋が塗料のバインダー(ビヒクル成分)として、使用されていたようです。
-
4-6江戸・黒船来航~明治時代イギリスで始まった産業革命と同様な大きな変化は日本では、黒船来航から明治維新にかけて現れます。鎖国が解かれて、政治体制が一気に変わり、鹿鳴館で代表される西洋文明が怒濤のごとく、日本に入ってきました。
-
4-7油性塗料時代 洋館旧岩崎邸の塗装片から見た塗料と塗装 1日本における塗料・塗装の変遷は次の様に進んできたと考えられる。A.塗料・塗装のルーツは漆塗りである(表4-1参照)
-
4-8油性塗料時代 洋館旧岩崎邸の塗装片から見た塗料と塗装 2前回の図4-10に塗膜断面の解析結果をまとめ、この中に
-
4-9ラッカー時代 (その1 木綿と硝化綿)4-7 塗料の変遷(その5) において、日本における塗料の変遷をA~Gのようであると示したが、ココで大きな忘れ物をしてしまった。それは硝化綿ラッカー(以降、NCラッカー)で代表される繊維素系塗料の存在をすっかり見落としたことである。
-
4-10ラッカー時代(その2 エアスプレーガンの誕生)日本では、第1次世界大戦後に残った火薬用NCの平和利用から塗料分野にNC(硝化綿、ニトロセルロース)が持ち込まれた。
-
4-11合成樹脂塗料時代 (その1 油とはどんな化合物か)本章は終盤を迎えており、今回より数回で、ラッカー時代に開始された工業塗装をさらに発展させた合成樹脂塗料について解説する。
-
4-12合成樹脂塗料時代 (その2 OPの塗料配合とSOPへの移行)1940年代から塗料用合成樹脂の代表になった油変性アルキド樹脂を4-12回と4-13回に分割して、紹介する。
-
4-13合成樹脂塗料時代 (その3 油を真似た油変性アルキド樹脂)今回ようやく、”油を真似て作られた合成樹脂塗料“の話ができることになり、嬉しい限りである。ところで、油を真似てとは、どんなことかを説明したい。
-
4-14合成樹脂塗料の発展連続被膜を形成する樹脂が塗膜の性能を大きく左右する。樹脂開発の経過は、表4-5(4-10掲載)で大まかに知ることはできるが、樹脂開発とそれに伴う塗料、塗装技術の変遷をまとめると、図4-29のように示される。13)
-
4-15合成樹脂塗料の種類別生産量の推移塗料は流動状態で被塗物を覆い、被膜を形成する。よって、塗料の必要条件は、(1)流動すること、(2)くっつくこと、(3)固まることになる。
-
4-16VOC削減型塗料-粉体とはどんな塗料なのか粉体塗装の事始めは鉄鋼をイオン化傾向の大きい亜鉛で被覆する金属溶射である。
-
4-17VOC削減型塗料-水性とはどんな塗料なのか前回の粉体塗料に比べると水性塗料には随分と親しみと言うか、近しいものを感じる。それは小学生の頃に水性塗料の仲間である水彩絵の具を使って居たこと、あるいは、木材を加工してくっつけるのに水性ボンドを使用した記憶があるからであろう。
第5章 塗料をより深く理解するために
-
5-1塗料(樹脂)選択の根拠について4章では、人類が時代と共に塗料とどのようにつき合ってきたのかを究明したく、塗料の変遷を取り上げてきた
-
5-2樹脂の成り立ち(その1)塗料用樹脂の特徴は、主鎖を形成する分子鎖の化学結合に依存する。例えば、図5-6に示すように、フタル酸樹脂(長油性アルキド樹脂)は主鎖がエステル結合からなるため、アルカリ性水溶液に浸漬すると、加水分解され、塗膜が溶解する。
-
5-3樹脂の成り立ち(その2)本稿では図5-14に示すエチレンやベンゼンのように2重結合を有する分子の成り立ちについて説明する。はじめに、エチレンとエタンとの違いは何かをまとめて見たい。
-
5-4塗料用樹脂のはなし(1)著者が感銘を受けた樹脂の教書は北岡協三氏の著書である。恐れ多いことであるが、エポキシ樹脂の成り立ち部分を一部、引用させて頂く。
-
5-5塗料用樹脂のはなし(2)主剤であるエポキシ樹脂(前回の図5-24)の両末端にはエポキシ基があり、硬化剤の有する活性水素H+と化学結合をして、クッキー塗膜を形成する。
-
5-6塗料用樹脂のはなし(3)前回の図5-30に示すポリアミド樹脂を固定し、エポキシ当量が一連に異なるS、M、Lを使用した塗膜の網目構造は、どのようになるのかを考えて見る。
-
5-7塗料用樹脂のはなし(4)2液型エポキシ樹脂塗料においては、主剤のエポキシ樹脂に対して反応する手の数が等しくなるように硬化剤のポリアミド樹脂が配合される。
-
5-8エポキシ樹脂(その2)準備中
-
5-9エポキシ樹脂(その3)準備中
-
5-10大型構造物の塗装系と樹脂の役割(その1)準備中
-
5-11大型構造物の塗装系と樹脂の役割(その2)準備中
-
5-12大型構造物の塗装系と樹脂の役割(その3)準備中
-
5-13塗料用アクリル樹脂入門(その1)準備中
-
5-14塗料用アクリル樹脂入門(その2)準備中
-
5-15塗料用アクリル樹脂入門(その3)準備中
-
5-16塗料用アクリル・シリコーン樹脂、ふっ素樹脂とは準備中